Why Does My Water Utility Need a Backflow Management Program
- Josh Ordway
- Sep 18, 2018
- 8 min read
Updated: Oct 9, 2018
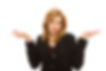
DO WATER UTILITIES NEED A BACKFLOW MANAGEMENT PROGRAM?
To answer the question simply…..YES 100% your Water Utility needs a backflow management program! But the question still stands, why does my Water Utility need a backflow management program. Many Water Utilities have operated for decades without having a program, and in many cases, if there is a program it is not running at maximum efficiency. So lets explore why water Utilities need backflow management programs.
Backflow prevention device management programs are often overlooked by water utilities across this country. That’s not to say that water utility managers are not doing their job, they just have so many other responsibilities they are forced to keep up with by regulatory agencies, that backflow prevention management often takes a back seat. This varies dramatically depending on what part of the country you are located in. It also depends on how strictly local, county, regional, and state level health departments or environmental protection agencies enforce backflow testing requirements. I have also found that some water utilities do not have the support of their governing regulatory agencies and therefore have a difficult time forcing their customers to test their backflow prevention devices on a regular basis. However, we are finding that is changing and changing rapidly!
WHAT IF MY WATER UTILITY DOES NOT HAVE A BACKFLOW MANAGEMENT PROGRAM?
Simple answer is: Get one and implement it as quickly as possible. This may seem like an overwhelming task, but you are not alone and there is help out there. Some of you might be thinking, “My regulatory agency isn’t forcing me to do anything and haven’t for years, so why should I make any changes?”. Trust me they will be implementing new requirements and it will be much simpler for you to be proactive now whether than having to get everything done in a rush at the last minute. If you find yourself in this position, refer to our article; Ten Steps to Starting/Maintaining a Backflow Management Program.
WHAT IF MY WATER UTILITY HAS A BACKFLOW PROGRAM BUT IT NEEDS TO BE IMPROVED?

Understanding your system’s weaknesses is the first step to making improvements. The ultimate goal of water utilities is to provide high quality safe potable water for their constituents, as efficiently as possible. Failed backflow prevention devices or locations requiring a device that go unprotected create a huge liability for the water utility. The owner of the property is typically responsible for purchasing and installing the backflow prevention device after submitting approved engineered plans to the water utility or municipality.
Additionally, it is the responsibility of the customer to maintain the device and have it tested on a consistent basis. Depending on the ordinances of the municipality, a test may be required annually or even more often like quarterly. If your water utility currently tests annually, then I would recommend maintaining that frequency of testing. If you are implementing a new backflow program, annual tests will suffice for most locations with a backflow preventer. Requiring more frequent testing can be done after your backflow program is running efficiently and a high percentage of your devices are in compliance.
The most important thing to understand is that the water utility is ultimately responsible for the safe distribution of drinking water and any contaminants that might enter the system. Therefore, if you think there might be a need for some improvements, you’re most likely correct and should act quickly to make those corrections. Maintaining your backflow program is also a continuous process and improvements or updates need to be made constantly. There have been many incidents where end user customers have been injured, poisoned, hospitalized, or worse due to the lack of a backflow prevention device or a non-functioning one.
WHAT CAN HAPPEN IF MY WATER UTILITY DOES NOT HAVE A BACKFLOW MANAGEMENT PROGRAM OR REFUSES TO MAKE IMPROVEMENTS AND UPDATES TO THE EXISTING ONE?
Below are some examples of recorded incidents caused by the lack of backflow prevention devices or situations where the mechanisms failed. You do not want your water utility to be in the media for having issues like the ones listed below.
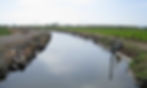
1. Residents in Eagle Sub-Division Get Sick from Drinking Irrigation Water
Eagle - The Center District Health Department has received 20-25 reports of Eagle residents getting sick from the water in the Corrente Bello Subdivision, the CDHD said it was likely a gastrointestinal illness.
Suez water and residents discovered that irrigation water from a nearby canal made it into several homes in the subdivision and that people in the neighborhood were drinking contaminated water.
My fifteen-year-old was sick, I was sick, two of my daughters were sick," said Karen Howell who has eight children. "I ran a bath for two-year-old and the water was brown." This neighborhood uses potable water for drinking, but they also have non-potable water that residents can use to water their lawns or their gardens, each home has what is called a backflow that acts as a fail-safe to prevent the irrigation water from mixing in with the drinking water in the homes.
Suez Water discovered one backflow in the neighborhood that got installed backward and said that was the cause of tainting the water in several Corrente Bello homes.
"Since 2012 we have had three similar cases, and in every case, it was the result of an improperly installed device by an unlicensed individual," said Marshall Thompson the general manager for Suez. Suez said they don't install the backflow devices, those are the homeowner's responsibility, however, Suez said it is important to get the backflow installed by a licensed company and to get it checked every year.
Residents did have their complaints about Suez during this whole process, mainly because one neighbor called the water company on July 14 after discovering brown water.
Suez said they responded with a technician who flushed the lines to that home, but they said they didn't find low levels of chlorine, a red flag for contaminated water because Suez uses chlorine to treat drinking water.
Suez called this an isolated incident and said it's not out of the ordinary to calls regarding brown water, the technician told the homeowner their water was safe.
Another neighbor called Suez back on July 18, this time around Suez did find low levels of chlorine and then discovered the improperly installed backflow device, then Suez flushed the system and collected samples to test the water. "Overall we responded in a timely manner," said Thompson. "Unfortunately, the water quality testing to verify the water sample takes two days to process."
On July 20 Suez alerted the residents that their water was safe, but they issued a boil advisory to let residents know that the water inside their homes was likely still contaminated. Suez said the residents needed to flush their plumbing system, turn their water heater to the highest setting, boil any water they were using in the home until the system was flushed and replace all their water filters.
"We are out one hundred dollars in filters," said Howell who was about to take her fifteen-year-old to the hospital. "I know people who have medical bills that they have to pay, and nobody says they are responsible for this, it is getting passed on to us." Howell also had complaints because she wanted to know what kind of bacteria her family was drinking, Suez did not test the contaminated water until after they flushed the lines.
We asked Suez who the homeowner was that had the backflow device that caused the problem, they told us they would not give out that information, in an effort to protect their customers. (https://www.backflowcases.com/2018/08/residents-in-eagle-subdivision-get-sick)
I have been in the water industry for over 12 years and have a deep respect for water professionals across this country. A majority of them do a great job but once in a while things happen that cannot be explained. However, I believe this particular situation could have been avoided. Suez indicated there was a backflow preventer at the property where the backflow occurred, but it was installed backwards. If a proper backflow management program was in place at this utility, I believe this situation would have never occurred.
Suez typically helps utilities manage their entire distribution system that are struggling with the resources to do so. Therefore, Suez might not have been operating this utility when the backflow device was installed at this location. A backflow device management program would have caught the improper installation of this particular backflow device if all the required steps of implementing a backflow management program were followed. Refer to our article 10 Steps to Implementing and Maintaining a Backflow Management Program. When the backflow device was installed, there should have been an initial inspection and test of the device after installation. During that process, it would have been discovered that the device was installed backwards! Very simple but somehow this device slipped through the cracks. Whether it was the Water Utility’s fault, or Suez’s fault for not properly testing the device after they took over the Water Utility, is not clear. Regardless people got sick and suffered the consequences. At the same time Suez, a great company, has their Integrity and competency questioned. All this could have been avoided with a good backflow management program.

2. Propane in the Water System Causes Fires
In August 1982, residents in a Connecticut town reported hissing, bubbling noises coming from washing machines, sinks, and toilets. Faucets sputtered out small streams of water mixed with gas. Propane gas had backflowed into the town’s public water system. Local firefighters and other official asked hundreds of residents to evacuate their homes and businesses.
The town provided water to a propane storage facility in the area. Water was furnished to the facility for both domestic use and fire protection and entered the facility through a single eight-inch-diameter service connection. The facility included 26 subsurface 30,000-gallon liquid propane storage tanks.
On the day of the backflow incident, workers needed to repair the storage tank at the propane storage facility. Before repairing the tank, workers had to purge the tank of residual propane. There are two common methods for purging liquid propane storage tanks. One method is to use an inert gas such as carbon dioxide. The other method is to use water. The use of water is the preferred method because it is a more positive method and will float out any sludge as well as gas vapors.
Accordingly, workers attempted to purge the tank using water in this case. They connected a hose to the tank from one of the two fire hydrants at the facility. Unfortunately, the pressure in the propane tank was about 85 to 90 psi, while the pressure in the town’s public water system was about 65 to 70 psi. Consequently, propane gas backflowed into the town’s public water system. It was estimated that about 2,000 cubic feet of gas flowed into the water system over a period of about 20 minutes. This is enough gas to fill approximately one mile of eight-inch diameter water main.
Fires were reported at two houses, and fire gutted one of these houses. At another house, a washing machine exploded. Police, propane company workers, and town water works personnel, however, limited damage and injuries by quickly sealing off the affected area. The town flushed fire hydrants and individual building plumbing systems and monitored for gas. The propane company promptly instituted revised propan tank purging procedures at is storage facility. (treeo.com – http://www.treeo.ufl.edu/backflow/epa-resources/backflow-case-histories/#a).
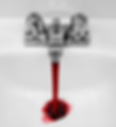
3. Blood in the Water Fountains (Careful if you have a weak stomach)
For some time, nurses at a Michigan hospital complained about rusty water coming from a hospital drinking fountain. When maintenance personnel finally looked into the matter, they discovered it was actually blood that the nurses were encountering at the drinking fountain. This blood had backflowed into the hospital’s potable water system from an autopsy table.
Hospital autopsy tables have a sump to collect blood and washing from the autopsy procedure. These tables also have a hose-spray unit for washing off organs, etc. On an autopsy table at the Michigan hospital, there was no hook to hang up the hose-spray unit, so pathologists placed the unit in the table sump when they were not using it. There also was no vacuum breaker in the water supply line to the hose-spray unit on this table, and the hospital had severe back-siphonage problems. Therefore, blood and other washing from the autopsy table were sucked into the hospital’s potable water system. The drinking fountain where the nurses were encountering the blood was about two doors from the autopsy room. (treeo.com – http://www.treeo.ufl.edu/backflow/epa-resources/backflow-case-histories/#a)
The incidents go on and on. In some of the cases there was blatant negligence, others were existing situations that were either left un-inspected, or officials were just un-aware of. Regardless, if your utility is not being pro active to either implement a backflow management program or continuously survey the existing system to make improvements, an incident will happen, and someone will be held accountable! Don’t be that person sitting on their hands when you are aware that changes need to happen! VEPO CrossConnex is able to help your Water Utility no matter what status your backflow management program is at. Contact us to SCHEDULE A DEMO.